|
Modellbau
Technik |
mini-sail
e.V. |
mb-02-20.htm; 07.2002
Ballastgewicht und Transportkiste
am Beispiel der ATLANTIS von Robbe.
Baubericht von Reinhart Thalheim
Probleme:
- Hohes Transportgewicht des Modells: ca. 18 kg
- Problematisches Gießen des Bleis in Formen,
Ziele:
- Bleigewicht
- Möglichkeit zur Anpassung an verschiedene Windverhältnisse
- Leichte, spätere Änderung des Bleigewichts zur Trimmung bei Umbauten
- Gesamtdichte fast wie gegossenes Blei
- Transportkiste:
- Leicht, stabil, witterungsbeständig
- Transport auf dem Autodach möglich
- Einmanntransport, vor allem durch Türen, wenn senkrechte Stellung der Transportkiste
notwendig
- Ohne Werkzeug durch einfaches Stecken zerleg- und in einer Wohnung verstaubar
Lösungen:
- Kalte Fertigung des Bleigewichtes:
- Bleiblech vom Dachklempner, 2 mm stark, etwa 3,- DM pro kg, ich mußte allerdings eine 50 kg
Rolle bei einer Einkaufs- und Liefergenossenschaft abnehmen.
- Auf in Kielraum eingelegtem Papier die Umrisse zeichnen
- Bleiblech mit kräftiger Schere ausschneiden
- Vorgang so lange wiederholen, bis die Stapelhöhe ausreichend groß ist
- Dabei mehrere Stücke anfertigen: leichteres Einfädeln, Anpassen an Windverhältnisse
möglich
- Bohrung und Verschrauben mit Senkschrauben
- Je Bleigewicht zwei Bohrungen für Faden zum sprichwörtlichen Einfädeln der Bleigewichte
- Wenn alle Teilstücke an der tiefsten Stelle des Kiels eine große durchgängige Bohrung
erhalten, so kann von oben ein Ms-Rohr mit aufgesetztem Gummiball, Sanitär-/Orthopädiehandel, zum
Absaugen des Wassers angesetzt werden, ohne die Bleigewichte auszubauen.
Bild 1
Das Aussehen der Bleigewichte ist natürlich um Einiges besser, wenn gleich ein klarer Plan
gegeben ist. Ich habe einiges probiert und das sieht man. Letztlich kann das Blei noch mit Farbe
o.ä. beschichtet werden, denn gesundheitlich ist es nicht unbedenklich.
Einmal war ich zu faul, die Bleigewichte aus dem Rumpf zu nehmen, nie wieder! Der Transport im
Werkzeugkoffer ist schon anstrengend genug.
Bild 2
Zusätzlich:
- Fertigung des Haltewinkels gegen Verrutschen der Bleigewichte, im Bild 3 zur besseren Ansicht
auseinandergezogen, der oberer Aluwinkel muß natürlich unter den Kopf der Feststellschraube:
- Zwei Aluwinkel: 20x15x3, 120 lang,
- Oberer Aluwinkel mit Langloch, unterer mit 2x M4 Gewinde
Einbau:
- Lösen der Feststellschraube und Zusammenschieben der Aluwinkel
- Einfädeln der verjüngten Enden in die Aussparungen der senkrechten Wandteile
- Auseinanderschieben der Winkel und Anziehen der Feststellschraube
- Leichtes Anziehen der Druckschraube, M4x60, gegen das obere, längere Bleigewicht
Bild 3
Vorraussetzung: Anderes Innenleben zum Durchfädeln der Gewichte,
Bild 4
Bild 4: Mit Vorliebe verwende ich zum Innenausbau Alu-Profile, weil durch die
Verwendung von Schrauben vor allem Inbusschrauben auch an diffizilen Stellen wiederholt Montagen
möglich sind. Die Gewinde halten doch erheblich besser und Änderungen sind nach dem Herausnehmen
des Gestells leicht möglich!
Auf Bild 4 am Beispiel der Segelwinde für die Umlaufschot zu sehen. Die grauen, geschlitzten
Kunststoffisolationsrohre aus der Elektrobranche sind seitlich verschiebbar und schützen die
Umlaufschot vor dem Hängenbleiben.
Bild 5
Fertigung der Transportkiste:
- Zusammenbau:
- Außenmaße: BxHxT 1450x450x430
- In die Gegenlager der Grundplatte die hintere Seitenwand, die zwei Stirnseiten und die
vordere Seitenwand stecken.
- Anschließend die Polystyrolblöcke einbringen.
- Dadurch hält das Ganze schon so zusammen, daß der Rumpf eingesetzt werden kann.
- Darauf kommen dann die Gegenplatten, die die Seitenteile um 2-3 mm in der Höhe
überragen.
- Durch den Druck stehen die Seitenteile etwas nach außen, so daß sich der aufgesetzte Deckel
durch leichtes Andrücken der Seitenteile in die Gegenlager der Seitenteile schieben läßt.
- Die zwei Spanngurte im Bereich der Polystyrol-Gegenplatten um die Transportkiste legen und
festzurren. Erstaunlich leicht und stabil!.
- Extra Griffe oder Schlaufen habe ich keine, die Finger unter die Spanngurte geschoben und
schon kann der Transport, auch senkrecht, durch Türen und Treppenhaus zum Auto von einer Person
bewältigt werden. Gesamtgewicht Modell und Kiste etwa 19 kg.
Bild 6 ==>
- Material:
- Pappelsperrholz: 5mm
- Aluwinkel Außenkanten:
- 20x15x2 mm, an Deckel und Boden außen umlaufend, langer Schenkel zu den Seitenteilen hin, an
Vorder- und Hinterseitenteil nur die senkrechten Seiten, Stirnseiten ohne
- Aluwinkel Gegenlager:
- 10x10x2, 50 lang,
lichter Abstand zum Außenwinkel Stärke des Sperrholzes plus 1mm, zum leichteren Einfädeln gut
angeschrägt bzw. im Schraubstock auf etwa 85° gebogen und mit je zwei Schrauben verschraubt. - 32
Stück
- Boden und Deckel: je 4 für Längsseiten und je 2 für Schmalseiten
- Vorder- und Hinterseitenteil: je 2 für Stirnseiten selbst ohne Gegenlager
- Polystyrol:
- 50mm stark, je zwei Platten zusammengeklebt, im Bug- und Heckbereich also je vier Platten.
Gegenplatte im Bug- und Heckbereich, Höhe 2-3 mm größer als das Höheninnenmaß, nimmt als
Gegenstück den Druck der Spanngurte auf und fixiert den Rumpf. Aussparungen des Polystyrols, die
mit dem Modell in Berührung kommen, mit Filz oder Schaumstoff auskleiden, sonst gibt es
Scheuerstellen.
- Anstrich:
- Dickschichtlasur, unbedingt auch innen lasieren, sonst verzieht sich das Holz.
- Zwei Spanngurte mit Ratsche, gleichzeitig Transportgriffe
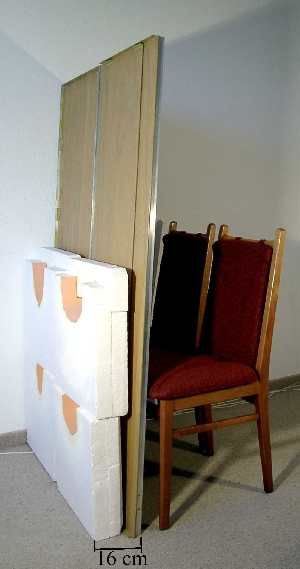
Bild 7
==>
Die zerlegte Transportkiste benötigt eine Grundfläche von nur 16x90cm,
da findet sich bestimmt ein Plätzchen in der Wohnung.
- Erreichte Gewichte in kg (+/- 100g Toleranz):
- Schiff, ohne Segel 8,6
- TK, Tara: 9,5
- Segeltasche: 2,5
- Ballastgewicht, eingeklebt: 1,7
- Ballastgewicht 1: 1,4
- Ballastgewicht 2: 2,0
- Ballastgewicht 3: 2,0
- Ballastgewicht 4: 3,6
- Ballastgewicht, kpl: 9,0
Bild 8
Erfinder und Konstrukteur der Transportkiste in Niedermoos 2002
Ich hoffe, daß die beschriebenen Lösungen einige Anregungen geben
können.
Reinhart Thalheim